Remember the 1983 Wendy’s commercial that had an actor that said “Parts is Parts"?
We all knew it wasn’t true for chicken, so why do some people think “parts is parts” for purchased parts in manufacturing?
Well to be frank, most supply chain professionals do understand that purchased parts have many different characteristics that impact how they are managed. At minimum, most materials managers will assign an ABC classification to parts that may impact how they are planned and ordered, what safety stock is carried, how often the parts are cycle counted, what types of PO’s or vendor agreements are used and many other considerations.
Unfortunately many material managers miss some of the most important considerations when looking at the part characteristics, or what we at Ultriva call a “part profile”. The part profile includes variability of consumption, lead-times, minimum order quantity or ideal container and/or container quantity, average daily usage and supplier delivery performance for that part.
The reason the part profile is so important is that it provides the planner with the answer to two key questions:
- What is the appropriate method of material replenishment for that part?
- What is the ideal quantity of the part to carry in inventory to support the profile?
By answering these two questions the company is ensured of having the shortest replenishment time for the part, with the easiest method of collaborating with the supplier and with the minimal inventory investment required.
Let’s break down the characteristics that make up the part profile.
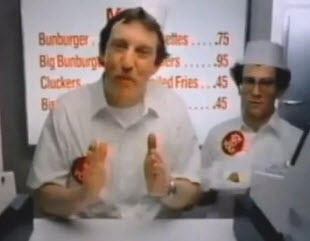
Variability of Consumption or S/X Ratio is an important consideration. We typically take ahistorical look at the past years consumption and receipt data for that part. We then compare the two to determine its S/X ratio. If the S/X Ratio is low, the part is likely a candidate for a consumption based replenishment method such as eKanban, Min/Max or Consigned Inventory.
Lead Times that are analyzed are the lead time to acknowledge orders, lead time to fulfill the order and the transit time from shipment to receipt. This breakdown in terms of the part’s lead times provide the basis for more effective part management and facilitates improved supplier performance.
Minimum Order Quantity is a critical characteristic and has an impact regardless of whether the part is replenished based on eKanban, MRP or any other method. If the part is a candidate for consumption based replenishment, then the Ideal Container and Container Quantity become critical. This characteristic is usually coupled with additional Plan for Every Part (PFEP) considerations.
Average Daily Usage and Supplier Performance are both characteristics that are considered when finalizing the appropriate inventory position to carry to support the Replenishment Methodology, Lead Times and Order Quantity baselines. Ultriva uses a standardized process along with their patent pending Inventory Optimization Tool to determine your part profiles and segment demand using your MRP/ERP data. Register for a FREE Inventory Optimization Assessment today.
As we learned almost 30 years ago….Parts are not Parts.
Bill Swisher
Ultriva, Inc. | Director of Business Development and Chicken Sandwich Lover